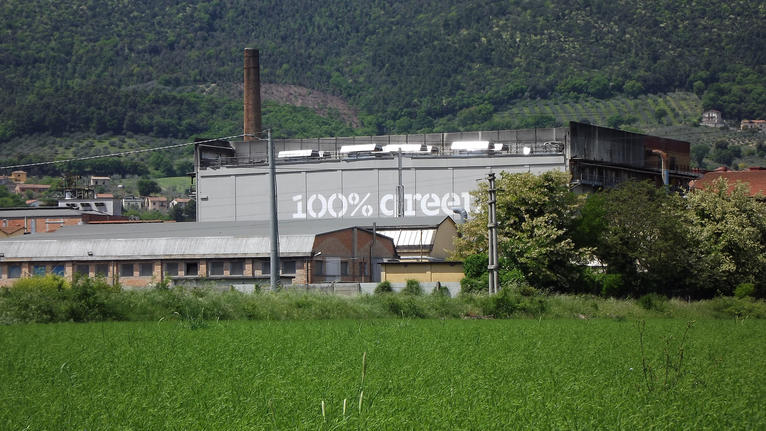
Nous agissons pour réaliser nos objectifs de développement durable dans notre usine verte de linoléum
En 2015, les Nations Unies ont adopté un ensemble de 17 objectifs en matière de développement durable. Chacun de ces objectifs fournit aux entreprises des directives pour les aider à contribuer à un meilleur avenir pour la planète tout en restant bénéficiaires. Voici quelques-unes des méthodes utilisées par Tarkett dans son usine verte de linoléum de Narni (Italie) pour atteindre ces objectifs de développement durable.
L'usine verte de linoléum de Narni est un mariage réussi entre héritage et innovation.
Le linoléum Tarkett est fabriqué dans l'usine de Narni en Italie depuis 1898. Narni est située sur l'ancienne via Flaminia, et ce sont les Romains qui fortifièrent son emplacement stratégique surplombant les étroites gorges de la Nera. À la fin du XIXe siècle, la présence du chemin de fer et de l'eau de la Néra, d'un sol fertile pour cultiver le lin et sa position centrale en Italie firent de Narni un site idéal pour la production du linoléum.
Construite en 1889, l'usine fut ensuite acquise par Giovan Battista Pirelli avant de devenir en 1898 la Società Italiana del Linoleum. Le groupe Sommer racheta l'usine en 1987 et fusionna avec Tarkett en 1997. Depuis, Tarkett n'a cessé d'améliorer ses processus de production et d'innover pour faire de Narni une usine verte qui cherche à rendre ses processus de production toujours plus respectueux de l'environnement. L'efficacité de la production et la qualité des produits n'ont cessé de s'améliorer. Aujourd'hui, l'usine est certifiée ISO 9001 (Système de qualité) et détient d'importantes certifications environnementales, dont ISO 14067 (gaz à effet de serre – empreinte carbone des produits), ISO 50001 (système de gestion énergétique), ISO 14001 (système de gestion environnementale), OHSAS 18001 (système de gestion de la santé et de la sécurité) et SA 8000 (responsabilité sociétale).
Nos équipes de Narni prennent des initiatives durables dans différents domaines.
Production avec de bons matériaux
Le partenariat avec les agriculteurs locaux a permis la culture locale de lin dans les champs entourant l'usine de Narni. Un des objectifs à court terme de l'unité de production est de collaborer avec des agriculteurs locaux pour augmenter la production locale de lin et ainsi réduire son empreinte carbone en utilisant plus de matières premières locales.
Les parcelles locales sont cultivées de façon responsable et durable, sans utiliser d'engrais chimiques. La pression des graines pour produire de l'huile de lin selon les spécifications techniques en vigueur pour notre production de revêtements de sol est assurée par des entreprises locales.
Produire pour les gens et prendre soin d'eux
La ligne de mélange
- À Narni, les matières premières manipulées pendant le processus de production sont sûres. Elles satisfont ou excèdent les réglementations et standards européens et proviennent de fournisseurs qualifiés et durables. Pour plus d’informations à propos des réglementations européennes sur les matières sûres, lisez l'article 33 du règlement REACH (règlement de l'Union européenne CE1907/2006).
- Il y a une augmentation continue de l'utilisation de matières renouvelables et recyclables. 94 % des matières sont naturelles, 78 % renouvelables, 100 % sont recyclables. Cet aspect contribue au bien-être et à la santé des ouvriers travaillant sur la ligne de mélange.
Postcombustion pour réduire les émissions de COV
- Trois dispositifs de postcombustion ont été installés pour réduire les émissions de composés organiques volatiles.
- Plus de 95 % de ces émissions de COV ont été réduites, diminuant l'impact de ces composés sur la santé du personnel.
Utilisation responsable des ressources
Différents types d'équipements ont été installés dans l'usine pour réduire la consommation de ressources naturelles ; ils ont également eu un impact positif sur le processus de production.
- L'usine a été équipée de trois échangeurs de chaleur pour récupérer la chaleur de l'oxydation de la postcombustion, de la ligne de postcombustion et des émissions de la chaudière à gaz. Cela a permis de réduire la consommation de gaz de 804 782 m³/an.
- Un sécheur d'air chauffe et déshumidifie l'air fourni à l'intérieur des fours. Ce système est actuellement étendu à un plus grand nombre de fours et permet :
- de réduire de 7 jours le temps nécessaire au séchage des revêtements de sol en linoléum,
- de réduire la consommation de gaz des fours de 59 136 m³/an
- de réduire les émissions de CO2 de 117 tonnes/an - Lors du calandrage, les déchets, les rebuts et les produits en fin de vie entrent dans un cycle biologique et technique. Le cycle fermé que nous implémentons permet de récupérer de la pâte de linoléum ainsi que du jute et des poudres qui sont réutilisés pour remplacer des matières premières vierges. Aucun déchet de production n'est mis en décharge.
- Une chaudière à biomasse a été installée : elle est alimentée par des biomasses internes qui produisent de l'eau chaude permettant de chauffer les fours. La chaudière à biomasse permet :
- de réduire la consommation de gaz des fours de 278 540 m³/an
- de réduire les émissions de CO2 de 552 tonnes/an - Le four est thermiquement isolé pour augmenter l'efficacité énergétique de l'usine. L'isolation est actuellement étendue à tous les autres fours. Cette isolation permet :
- de réduire la consommation de gaz des fours de 106 000 m³/an
- de réduire les émissions de CO2 de 215 tonnes/an
- de réduire de 2 jours le temps nécessaire au séchage des revêtements de sol en linoléum pour chaque four. - Le système de trigénération consiste en la production simultanée d'électricité, de chauffage et de refroidissement à partir d'un seul appareil (moteur à gaz). En refroidissant les gaz d'échappement du moteur, on peut obtenir des températures élevées qui peuvent être utilisées pour la production d'eau surchauffée destinée au séchage dans les fours. La chaleur récupérée dans le circuit de refroidissement est utilisée pour générer de l'eau chaude. Ce fluide alimente une unité de réfrigération par absorption qui produit de l'eau froide à 17 °C. Cela permet :
- Efficacité en hausse de la production thermique et électrique
- Réduction des émissions de CO2 (de 184 tonnes/an) - Le département recyclage récupère les chutes post-production et post-installation. Grâce à cette action, les chutes éliminées ont été réduites de 70 % depuis 2007 et 1 600 000 kg de poudre de linoléum sont réutilisés dans le processus pour remplacer des matières premières vierges.
- 3 circuits d'eau fermés ont été installés dans le département oxydation, la ligne de coupe et la ligne de mélange. Grâce à ces cycles fermés, 100 % de l'eau industrielle utilisée dans le processus de production est soit recyclée, soit recirculée.
- Un évaporateur récupère la condensation provenant des compresseurs. Le cycle d'eau fermé permet de récupérer l'eau de l'évaporateur afin de l'utiliser pour le nettoyage de l'oxydateur. En tout, cet équipement nous a permis de réduire notre consommation d'eau de 80 000 litres/an.
- Le toit du bâtiment abritant le bureau technique et le laboratoire R&D est équipé d'un système photovoltaïque. Celui-ci a permis de réduire la consommation électrique du bâtiment de 65 000 kWh/an et les émissions de CO2 de 29 tonnes/an.
- Un système géothermique basse enthalpie a été construit pour être intégré dans le chauffage/refroidissement existant du bâtiment de bureaux. Ce système a permis de réduire les émissions de CO2 de 124 tonnes/an et la consommation de gaz de 61 806 m³/an.
- Une récupération des eaux pluviales a été organisée pour toute la surface couverte par l'usine (26 190 m²). Cela permet le stockage immédiat d'eau fraîche, l'eau potable étant remplacée par l'eau de pluie dans le processus de production. La récupération des eaux pluviales permet également d'éviter de saturer les réseaux d'égout en cas de forte pluie.
C'est ce que nous faisons actuellement dans notre usine verte afin que les revêtements en linoléum soient durables tant pour les gens qui les produisent que pour les gens qui les utilisent.
Nos objectifs à l'horizon 2020 ?
- Doubler le volume de linoléum post-installation ou post-client collecté par rapport à 2010
- Maintenir 100 % d'eau industrielle recyclée/recirculée (circuit fermé)
- Réduire de 60 % la production de gaz à effet de serre par rapport à 2010 - Diminuer de 28 % la consommation énergétique (KWh/m²) par rapport à 2010
Vous êtes intéressé par les initiatives que nous avons prises dans notre usine de linoléum de Narni ?